
|
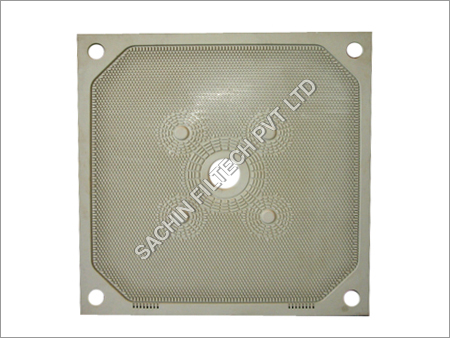
Membrane Filter Plates
Product Details:
X
Product Description
Membrane Filter Plates
Membrane filter press plates utilize an impermeable, flexible member attached to the filter press plate core. This terminology should not be confused with submicron "membranes" used in ultra filtration or reverse osmosis. In filter presses, a membrane, also called a diaphragm, is designed to inflate by compressed air or pressurized water to squeeze residual moisture out of the formed filter cake. Polypropylene membrane plates supplied in FILTER PRESS INDIA Filter Presses have been in use for more than ten years with significant success. Theses plates are currently in many severe applications - some operating two cycles per hour, 24 hours per day for two years - tens of thousand of cycles without failure.
Membrane Filter Press Provides
Membrane filter press plates utilize an impermeable, flexible member attached to the filter press plate core. This terminology should not be confused with submicron "membranes" used in ultra filtration or reverse osmosis. In filter presses, a membrane, also called a diaphragm, is designed to inflate by compressed air or pressurized water to squeeze residual moisture out of the formed filter cake. Polypropylene membrane plates supplied in FILTER PRESS INDIA Filter Presses have been in use for more than ten years with significant success. Theses plates are currently in many severe applications - some operating two cycles per hour, 24 hours per day for two years - tens of thousand of cycles without failure.
Membrane Filter Press Provides
-
Reduced Cycle Time
-
Improved Cake Washing
-
Highest Cake Solids
Reduced Cycle Time: Conventional filter presses filter only 75-80% of the batch in the first 50% of the cycle time. If the plate stack is opened before the full cycle is complete, the result is a wet, sloppy cake.
A Membrane Filter Press, however, can be stopped at the most efficient point in its cycle. By applying pressure to the membrane built into the filter plate, the cake is squeezed to achieve final solids content in a significantly reduced cycle time.
Improved Cake Washing: FILTER PRESS INDIA Membrane Filter Presses improve cake washing by initiating a low-pressure pre-squeeze before the wash cycle is begun. This pre-squeeze eliminates channeling (cracks and less well-formed areas of the cake) and produces a uniform, homogeneous filter cake and optimum wash efficiency.
Highest Cake Solids: By applying a high pressure squeeze to the filter cake you produce the final cake with solids content from 50 to 100% greater than can be achieved with conventional filter presses. This is important for both maximum yield, where a high value liquid is your product, or high solids-content, where reduced moisture in the final cake is critical.
A FILTER PRESS INDIA Membrane Filter Press provides a dryer cake than can be obtained using high feed pumping pressure in a conventional filter press. It significantly reduces or eliminates downstream thermal drying and associated costs in energy and time.
Corner-Feed for Better Filtration : FILTER PRESS INDIA recommends corner-feed plates because of their numerous design advantages for virtually every filter press installation. FILTER PRESS INDIA features this design in its Membrane Filter Presses as well as in conventional filter presses.
Corner-feed design offers the most efficient cake formation and provides even solids distribution through-out the plate stack. More importantly, eliminating a center-feed eye allows construction of a stronger plate requiring no supporting stay bosses which hamper thorough cake washing and cake discharge.
With a center-feed filter plate, cake washing is difficult due to wash water "short circuiting" through the open center-feed eye. Corner-feed is the only plate design which insures thorough cake washing integrity.
Membrane Filter Plates
The membrane squeeze plate is offered to suit up to 435 psi / 30 bar squeezing pressure. Due to additional liquid extraction during the squeeze cycle, solid percentages increases. Filtration cycle time are reduced compared to the conventional recess chamber plate (Plate and frame) filter press, resulting in Benefits of membrane plates v/s chamber plates. Conventional type filter presses are limited to using feed pump discharge pressure to produce dry solids, resulting in longer cycle times.
The membrane squeeze plate reduced the long packing cycle by introducing a squeeze medium in to the center of the membrane squeeze plate. This allows the membranes to flex against the cake, compressing and packing it. Filtration cycle are shorter, dry solids are increased, and waste volume is reduced.
This membrane are designed to de water the most difficult sludge and protect the plates against potential cake less chambers.
The high pressure membranes were developed for difficult filtration processes. Extreme squeeze pressure are possible due to the combination of the special feed inlet design and selected special materials.
Features & Benefit Of Membrane Plate V/S Chamber Plate
A Membrane Filter Press, however, can be stopped at the most efficient point in its cycle. By applying pressure to the membrane built into the filter plate, the cake is squeezed to achieve final solids content in a significantly reduced cycle time.
Improved Cake Washing: FILTER PRESS INDIA Membrane Filter Presses improve cake washing by initiating a low-pressure pre-squeeze before the wash cycle is begun. This pre-squeeze eliminates channeling (cracks and less well-formed areas of the cake) and produces a uniform, homogeneous filter cake and optimum wash efficiency.
Highest Cake Solids: By applying a high pressure squeeze to the filter cake you produce the final cake with solids content from 50 to 100% greater than can be achieved with conventional filter presses. This is important for both maximum yield, where a high value liquid is your product, or high solids-content, where reduced moisture in the final cake is critical.
A FILTER PRESS INDIA Membrane Filter Press provides a dryer cake than can be obtained using high feed pumping pressure in a conventional filter press. It significantly reduces or eliminates downstream thermal drying and associated costs in energy and time.
Corner-Feed for Better Filtration : FILTER PRESS INDIA recommends corner-feed plates because of their numerous design advantages for virtually every filter press installation. FILTER PRESS INDIA features this design in its Membrane Filter Presses as well as in conventional filter presses.
Corner-feed design offers the most efficient cake formation and provides even solids distribution through-out the plate stack. More importantly, eliminating a center-feed eye allows construction of a stronger plate requiring no supporting stay bosses which hamper thorough cake washing and cake discharge.
With a center-feed filter plate, cake washing is difficult due to wash water "short circuiting" through the open center-feed eye. Corner-feed is the only plate design which insures thorough cake washing integrity.
Membrane Filter Plates
The membrane squeeze plate is offered to suit up to 435 psi / 30 bar squeezing pressure. Due to additional liquid extraction during the squeeze cycle, solid percentages increases. Filtration cycle time are reduced compared to the conventional recess chamber plate (Plate and frame) filter press, resulting in Benefits of membrane plates v/s chamber plates. Conventional type filter presses are limited to using feed pump discharge pressure to produce dry solids, resulting in longer cycle times.
The membrane squeeze plate reduced the long packing cycle by introducing a squeeze medium in to the center of the membrane squeeze plate. This allows the membranes to flex against the cake, compressing and packing it. Filtration cycle are shorter, dry solids are increased, and waste volume is reduced.
This membrane are designed to de water the most difficult sludge and protect the plates against potential cake less chambers.
The high pressure membranes were developed for difficult filtration processes. Extreme squeeze pressure are possible due to the combination of the special feed inlet design and selected special materials.
Features & Benefit Of Membrane Plate V/S Chamber Plate
- Shorter cycle time
- Increased dry solids
- Reduced filtration time
- Easily replaceable
- Membrane are common and cab be used on either side of the plate
- Pip style drainage surface design for uniform flex.
- Reduced cake washing time
- Lesser wash water consumption
- Increased capacity
- Lower waste disposal cost
- Lower operating cost
- Excellent cake discharge
- Higher quality and valued end product
How Membrane Plates Works
Membrane plates are constructed in the same basic method as the recessed chamber plates. The drainage surface of the plates, however, are flexible. After filtration, when the chamber are filled with solids and while the filter press is stilled, air pressure is exerted behind the flexible drainage of the plate. The membrane in turn inflates or flexes outward and exert pressure on the filter cake which have been formed. The cakes are then squeezed to reduce the amount of remaining moisture prior to cake discharge.
Membrane plates are constructed in the same basic method as the recessed chamber plates. The drainage surface of the plates, however, are flexible. After filtration, when the chamber are filled with solids and while the filter press is stilled, air pressure is exerted behind the flexible drainage of the plate. The membrane in turn inflates or flexes outward and exert pressure on the filter cake which have been formed. The cakes are then squeezed to reduce the amount of remaining moisture prior to cake discharge.
- Contact Details
GST : 24AAFCS5905E1ZL
- Sachin House, Plot No. 77-4, F-Road, Phase-I, GIDC Estate, Vatva, Ahmedabad - 382445, Gujarat, India
|
|
![]() |
SACHIN INDUSTRIES LIMITED
All Rights Reserved.(Terms of Use) Developed and Managed by Infocom Network Private Limited. |